Gold Plating vs Immersion Gold in PCBs
Introduction
When it comes to printed circuit boards (PCBs), there are various methods of applying a protective layer of gold. Two commonly used techniques are gold plating and immersion gold. While both methods serve the purpose of protecting the copper traces on the PCB, they differ in terms of their processes and characteristics. In this article, we will explore the differences between gold plating and immersion gold in PCBs.
What is PCB Immersion Gold?
PCB (Printed Circuit Board) immersion gold is a type of surface finish used in the manufacturing of electronic circuit boards. It is a process in which a thin layer of gold is deposited onto the surface of the PCB to protect it from oxidation and provide a reliable and durable connection for electronic components.
How Does PCB Immersion Gold Work?
The process of applying immersion gold to a PCB involves several steps:
- Clean the PCB: The PCB is thoroughly cleaned to remove any dirt, oils, or other contaminants that may be present on the surface.
- Apply a chemical solution: A chemical solution, typically a mixture of gold salt and a reducing agent, is applied to the surface of the PCB. This solution contains the gold ions that will be deposited onto the PCB.
- Electroless deposition: The PCB is immersed in the chemical solution, and a thin layer of gold is deposited onto the surface through a process called electroless deposition. This process does not require an external power source and ensures a uniform and even distribution of gold particles.
- Rinse and dry: Once the desired thickness of the gold layer is achieved, the PCB is rinsed to remove any excess chemicals and then dried.
What is Immersion Gold?
Immersion gold is a type of surface finish that is applied to the copper traces and pads of a PCB. It consists of a thin layer of gold that is chemically deposited onto the copper surface. The process involves several steps, including cleaning the copper surface, applying a layer of nickel, and then immersing the PCB in a gold bath.
The gold layer provides excellent conductivity and corrosion resistance, making it an ideal choice for PCBs. It also offers a flat and smooth surface, which is crucial for fine-pitch components and surface mount technology (SMT) assembly.
Why is Immersion Gold Widely Used in the PCB Industry?
Immersion gold has become a popular choice for PCB surface finish due to its numerous advantages and wide-ranging applications. Here are some reasons why it is widely used in the PCB industry:
- Reliability: Immersion gold provides a reliable and consistent surface finish, ensuring the long-term performance and durability of the PCB.
- Compatibility: It is compatible with various soldering and assembly processes, making it suitable for different manufacturing requirements.
- Industry standards: Immersion gold is widely recognized and accepted as a standard surface finish in the PCB industry. It meets the requirements of various industry specifications and certifications.
- Wide range of applications: Immersion gold is suitable for a wide range of applications, including consumer electronics, automotive, telecommunications, medical devices, and more.
- Cost-effectiveness: While immersion gold may be slightly more expensive compared to other surface finishes, its benefits outweigh the cost, especially for high-reliability applications.
Gold Plating in PCB
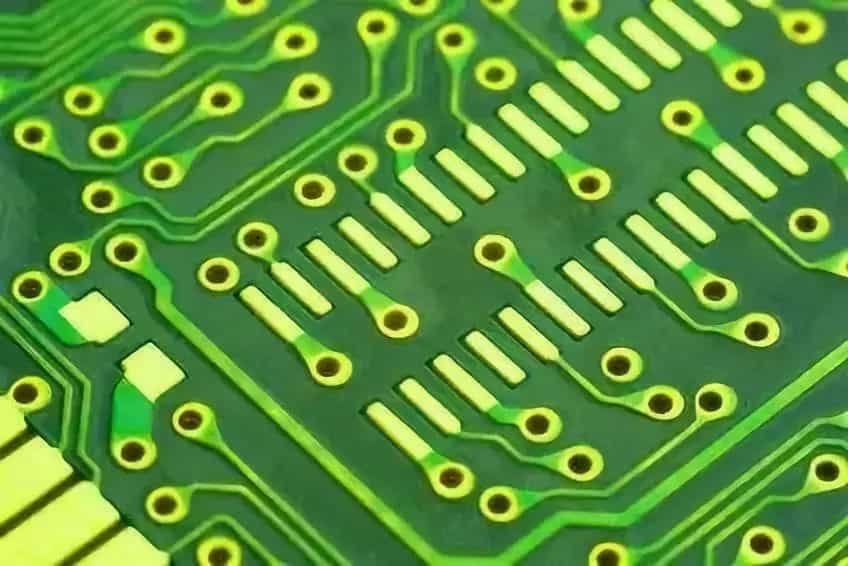
Gold plating is a process where a thin layer of gold is deposited onto the surface of the PCB. This is typically done by electroplating, where an electric current is used to coat the surface with gold ions. The thickness of the gold layer can vary depending on the requirements, but it is usually in the range of a few microns. One of the main advantages of gold plating is its excellent conductivity.
Gold is an excellent conductor of electricity, and it does not oxidize or corrode easily. This makes it ideal for applications where reliable electrical connections are crucial, such as in high-frequency circuits or in environments with high humidity or corrosive substances. Gold plating also provides a highly reliable and durable surface finish. The gold layer acts as a barrier against oxidation and corrosion, ensuring that the underlying copper traces are protected. This makes the PCB more resistant to wear and tear, extending its lifespan.
Immersion Gold in PCB
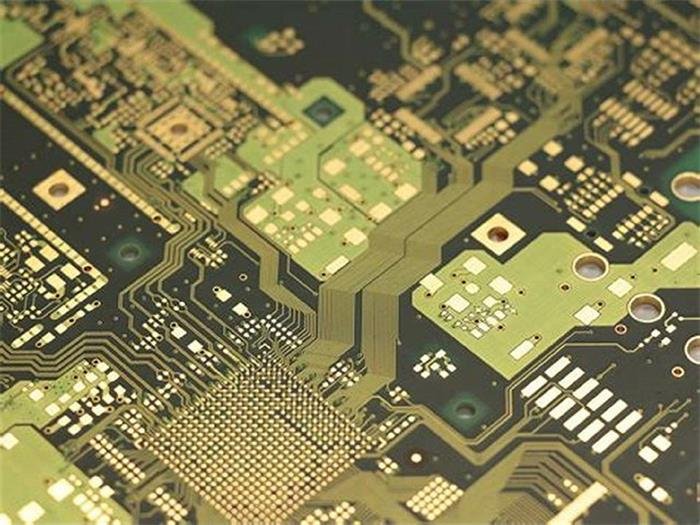
Immersion gold, also known as electroless gold plating, is a process where a thin layer of gold is deposited onto the surface of the PCB without the use of electricity. Instead, a chemical reaction is used to coat the surface with a layer of gold. One of the main advantages of immersion gold is its even and consistent thickness. Unlike gold plating, where the thickness can vary depending on the current and plating time, immersion gold provides a uniform layer of gold across the entire surface of the PCB.
This ensures that all the copper traces are equally protected, resulting in better performance and reliability. Another advantage of immersion gold is its flat and smooth surface. The gold layer is typically very thin, resulting in a smooth finish that is ideal for applications where surface mount technology (SMT) components are used. The flat surface allows for better solderability and improved performance of the components.
Comparison between Gold Plating and Immersion Gold in PCBs
Now that we have discussed the basics of gold plating and immersion gold, let’s compare the two methods based on different factors:
Process:
Gold plating involves the use of electricity to deposit a layer of gold onto the PCB surface, while immersion gold uses a chemical reaction. This difference in process affects the thickness, uniformity, and surface finish of the gold layer.
Thickness:
Gold plating allows for a thicker layer of gold, typically in the range of a few microns. On the other hand, immersion gold provides a thinner and more uniform layer, usually around 1-2 microns. The thickness requirement depends on the specific application and the desired level of protection.
Surface Finish:
Gold plating results in a slightly rougher surface compared to immersion gold. This can be advantageous in some applications where a rough surface is required for better adhesion of certain materials or for improved solderability. On the other hand, immersion gold provides a smooth and flat surface, which is ideal for SMT components.
Cost:
In terms of cost, gold plating is generally more expensive than immersion gold. The electroplating process requires more equipment and resources, making it a costlier option. Immersion gold, on the other hand, offers a more cost-effective solution without compromising on performance and reliability.
Applications:
Both gold plating and immersion gold have their own set of applications. Gold plating is commonly used in high-frequency circuits, connectors, and applications that require high reliability and durability. Immersion gold, on the other hand, is preferred for SMT applications, where a smooth and flat surface is crucial for the performance of the components.
Conclusion
In conclusion, gold plating and immersion gold are two popular methods of applying a protective layer of gold on PCBs. While both methods serve the purpose of protecting the copper traces and ensuring reliable electrical connections, they differ in terms of their processes, thickness, surface finish, cost, and applications. It is important to consider these factors when choosing the right method for your specific PCB requirements. Whether you opt for gold plating or immersion gold, both methods offer excellent protection and can enhance the performance and reliability of your PCBs.