Modbus Communication Protocol for Industrial Machines
Introduction
Modbus is one of the most widely used communication protocols in industrial automation, playing a critical role in connecting devices such as sensors, controllers, and actuators to facilitate efficient machine communication. Developed in 1979 by Modicon (now part of Schneider Electric), Modbus was originally designed for programmable logic controllers (PLCs). Today, it remains a key protocol for enabling interoperability between diverse industrial devices and systems, from manufacturing floors to power plants.
The protocol’s simplicity, flexibility, and compatibility with a wide range of equipment have made it a de facto standard in industries that require reliable data exchange in often harsh environments. As industrial automation moves towards Industry 4.0 and the Industrial Internet of Things (IIoT), Modbus continues to evolve, ensuring its relevance in modern, data-driven operations.
What is Modbus Communication Protocol?
Modbus is a serial communication protocol designed for transmitting information between electronic devices over various media such as RS-232, RS-485, and Ethernet. It operates in a master-slave architecture, where one device (the master) controls the flow of communication by sending requests to one or more slave devices, which in turn provide the requested data or perform specific tasks.
Key characteristics of Modbus include:
- Open and standard: Modbus is an open protocol, meaning it is free to use and widely adopted by equipment manufacturers.
- Simplicity: Its straightforward structure makes it easy to implement, configure, and maintain.
- Multi-device communication: Modbus can communicate with up to 247 slave devices using simple message framing.
How it Works in Industrial Machines
In an industrial setting, Modbus enables communication between controllers (such as PLCs) and field devices (sensors, actuators) over a serial bus or Ethernet. The master device sends a command that includes the type of operation (e.g., read, write) and the address of the data it wants to access from the slave. The slave device processes this command and sends the requested data back to the master or performs the specified action.
For example, in a manufacturing system, a PLC may use Modbus to communicate with a temperature sensor to monitor and adjust a heating process. This real-time communication ensures smooth control and monitoring of industrial machines.
Comparison with Other Industrial Protocols
Compared to other protocols like Profibus and Ethernet/IP, Modbus is simpler and more cost-effective. However, Modbus operates at lower speeds than Profibus and lacks the advanced diagnostic capabilities of Ethernet/IP. Additionally, Modbus was originally designed without security features, making it less secure than modern protocols unless additional layers like firewalls or encryption are applied.
Types of Modbus Protocols
Modbus RTU (Remote Terminal Unit)
Modbus RTU is the most common version of the Modbus protocol, typically used in serial communication over RS-485 or RS-232. It features a compact message structure that allows for fast data transmission. In RTU mode, the data is encoded in binary format, making it both efficient and reliable for long-distance communication in noisy industrial environments.
Advantages:
- Highly efficient for long-distance communication over serial lines.
- Simple and easy to implement with existing hardware.
Use cases:
- Suitable for control systems that require communication between PLCs and field devices in environments such as factories, power plants, and water treatment facilities.
Modbus TCP/IP
Modbus TCP/IP extends Modbus communication over Ethernet, allowing devices to communicate via the same network used for IT infrastructure. This protocol wraps Modbus messages in TCP frames, facilitating communication over larger distances and enabling the integration of industrial devices with modern networking technology.
Advantages:
- Seamless integration with Ethernet networks.
- Faster data rates and larger network coverage compared to RTU.
- Ability to connect multiple master devices.
Applications:
- Used in applications requiring integration with existing Ethernet-based networks, such as smart grids, building automation, and IIoT environments.
Modbus ASCII
Modbus ASCII transmits data in readable ASCII format, which is more human-readable but less efficient than the binary-based RTU format. It is suitable for communication over long distances but is generally slower due to the larger message size.
Differences from RTU:
- ASCII is easier to debug due to its readable format but is slower and less efficient than RTU.
- ASCII uses start and stop bits in message frames, which makes it less compact than RTU.
Use cases:
- Primarily used in systems where human readability of the data stream is necessary or beneficial for diagnostics.
How Modbus Works
Master-Slave Communication Model
In the Modbus protocol, communication occurs in a master-slave model, where a single master device (e.g., a PLC or computer) controls multiple slave devices (e.g., sensors, actuators, other controllers). The master initiates all communication by sending requests to the slave devices, which respond by sending the required data or performing the action requested.
Message Framing: Requests and Responses
Each Modbus message follows a strict format. A request from the master includes the slave address, function code (read/write), data to be written or the address of the data to be read, and a checksum. The slave responds with the requested data or an acknowledgment of the action.
- Request: [Slave Address] [Function Code] [Data] [Error Check]
- Response: [Slave Address] [Function Code] [Data or Acknowledgment] [Error Check]
Data Format and Addressing
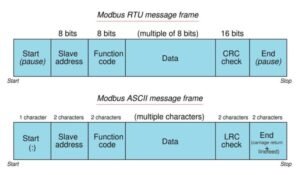
In Modbus, data is organized in registers. The most common types are:
- Coils: Discrete on/off values.
- Input Registers: Discrete inputs (read-only).
- Holding Registers: 16-bit values (read/write).
Addressing is important, as each device has a unique identifier, and data points within the device (e.g., sensor readings) are mapped to specific addresses within the slave’s memory.
Modbus Applications in Industrial Machines
Integration in PLCs, Sensors, and Actuators
Modbus is widely used to integrate PLCs, sensors, and actuators within industrial machines. PLCs often act as the master device, controlling field devices like temperature sensors, motor drives, and flow meters, all of which are connected via Modbus. This integration facilitates efficient control, monitoring, and automation of industrial processes.
Examples of Industries
- Manufacturing: Modbus is used for machine control, conveyor systems, and automated manufacturing lines.
- Power Plants: Used to monitor and control critical equipment like turbines and generators.
- Water Treatment Plants: Controls the operation of pumps, valves, and sensors to maintain water quality.
Advantages of Modbus in Industrial Systems
Interoperability and Flexibility
One of the most significant advantages of Modbus is its interoperability. As an open and widely supported protocol, Modbus allows seamless communication between devices from different manufacturers. Whether it’s PLCs, sensors, actuators, or human-machine interfaces (HMIs), Modbus can be easily integrated into various industrial systems, providing great flexibility in system design and deployment.
Simplicity and Cost-Effectiveness
Modbus is valued for its simplicity. Its straightforward communication model (master-slave) and easily understandable message structure make it simple to implement and troubleshoot. Additionally, since it operates over common industrial networks like RS-485 or Ethernet, the need for specialized hardware is minimal, making it cost-effective. Many manufacturers also offer Modbus-compatible devices, reducing the overall cost of system integration.
Scalability for Small to Large Systems
Modbus is scalable, accommodating systems ranging from small, simple configurations to large, complex industrial environments. It supports up to 247 devices on a single network (in RTU mode), making it ideal for both small and large industrial setups. This scalability ensures that Modbus can be used in everything from small factory installations to extensive, multi-location industrial systems.
Challenges and Limitations
Latency and Performance in High-Demand Environments
While Modbus is sufficient for many applications, it may face latency issues in high-demand environments where real-time performance is critical. For instance, Modbus RTU’s relatively slow data rates over serial connections can create bottlenecks in large, high-traffic systems, limiting its effectiveness in scenarios that demand rapid data exchange.
Security Concerns in Legacy Modbus Implementations
Security is a significant challenge for legacy Modbus systems. When Modbus was first developed, industrial cybersecurity was not a major concern, and as a result, early Modbus implementations lack encryption or authentication mechanisms. This makes Modbus networks vulnerable to unauthorized access or data manipulation, especially in the context of modern industrial threats such as cyberattacks.
Addressing the Need for Encryption in Modbus
To address security concerns, modern implementations of Modbus (such as Modbus TCP/IP) are increasingly being integrated with additional security measures, including encryption and firewalls. However, legacy Modbus systems often require upgrades or add-ons to ensure that communication is secure, making it essential for industrial users to assess the security of their Modbus-based networks.
Modbus Protocol Implementation
Hardware and Software Requirements
To implement Modbus, you typically need a master device (e.g., PLC or computer), slave devices (e.g., sensors or actuators), and communication media such as RS-485 (for Modbus RTU) or Ethernet (for Modbus TCP/IP). On the software side, many industrial control systems (SCADA, PLC software) come with built-in support for Modbus communication.
Common Tools and Libraries for Modbus Integration
Several software libraries and tools are available to simplify Modbus implementation:
- LibModbus: A popular open-source library for implementing Modbus in C.
- Modscan/Modsim: Tools for testing and simulating Modbus networks.
- Python libraries: Like PyModbus, for integrating Modbus into Python-based automation systems.
Steps for Configuring Modbus Communication in a Machine
- Select the Communication Type: Choose between Modbus RTU, ASCII, or TCP/IP depending on your network setup and application.
- Assign Device Addresses: Each slave device on the network must have a unique address for communication.
- Define Registers: Assign memory addresses (coils, input registers, holding registers) for each data point that needs to be communicated.
- Configure Master-Slave Relationship: Set up the master device to send requests and the slave devices to respond accordingly.
- Test the System: Use diagnostic tools to ensure that devices are communicating as expected and troubleshoot any issues.
Modbus Troubleshooting and Maintenance
Common Issues with Modbus Communication
Some of the common issues with Modbus communication include:
- Incorrect wiring or termination: Problems like signal degradation or noise can occur if RS-485 networks are not properly terminated.
- Address conflicts: If two devices share the same address, communication issues will arise.
- Timeouts and response delays: These are typically caused by network congestion or incorrect device configuration.
Best Practices for Monitoring and Troubleshooting
- Monitor Traffic: Use software tools to monitor Modbus traffic and detect any anomalies in communication.
- Check Network Configuration: Ensure that devices are properly addressed, and baud rates and data formats are correctly configured.
- Use Diagnostics Tools: Tools like Modscan allow for real-time monitoring and debugging of Modbus networks.
Tools for Diagnostics and Performance Analysis
Some popular tools for troubleshooting and performance analysis include:
- Wireshark: A network protocol analyzer that can capture and analyze Modbus TCP packets.
- Modpoll: A command-line tool for polling Modbus devices, useful for checking device response times.
- Modscan: A Windows-based tool to monitor Modbus communication on serial or TCP/IP networks.
The Future of Modbus in Industrial Automation
Adaptation to Modern Industry 4.0 and IIoT (Industrial Internet of Things)
Modbus continues to evolve in the context of Industry 4.0 and IIoT, where increased connectivity between machines and cloud-based systems is essential. The protocol’s simplicity and widespread adoption make it a candidate for continued use, particularly when integrated with modern communication technologies like MQTT and OPC-UA, which provide the ability to transmit Modbus data to higher-level applications.
Integration with Advanced Networking Technologies
As industries move toward smarter systems, Modbus is increasingly being used alongside Ethernet, Wi-Fi, and even 5G networks. This integration allows Modbus devices to communicate in real-time across vast distances, making it easier to monitor and control distributed industrial systems. Additionally, Modbus gateways and converters are being developed to integrate Modbus systems with modern industrial networks, allowing legacy systems to adapt to new technological demands.
Conclusion
Modbus has stood the test of time as one of the most reliable and versatile communication protocols in industrial automation. Its simplicity, widespread support, and ability to integrate with modern technologies make it an essential tool for efficient machine communication in industries ranging from manufacturing to energy. While challenges such as security and performance in high-demand environments exist, solutions like Modbus TCP/IP and encryption techniques are helping overcome these limitations. As industrial automation evolves toward Industry 4.0 and IIoT, Modbus will continue to play a crucial role, adapting to the ever-changing demands of modern industrial systems.
Frequently Asked Questions (FAQs)
What types of devices support Modbus?
Modbus is supported by a wide range of industrial devices, making it highly versatile for automation systems. Common devices that support Modbus include:
- Programmable Logic Controllers (PLCs)
- Human-Machine Interfaces (HMIs)
- Industrial sensors and actuators such as temperature, pressure, and flow sensors.
- Motor drives for speed control in industrial machinery.
- Remote Terminal Units (RTUs) and Supervisory Control and Data Acquisition (SCADA) systems. Many manufacturers offer Modbus support as a standard feature in their equipment, allowing easy communication between different devices within an industrial network.
How secure is Modbus communication?
Modbus was originally designed with simplicity in mind, and security was not a primary concern. As a result, legacy Modbus protocols (such as Modbus RTU and Modbus ASCII) do not have built-in encryption or authentication mechanisms, making them vulnerable to eavesdropping, tampering, and unauthorized access.
To improve security, modern implementations like Modbus TCP/IP can be paired with additional security measures such as:
- Firewalls to block unauthorized access.
- VPNs for secure remote communication.
- Encryption protocols like SSL/TLS to protect data integrity and confidentiality. It is essential to implement additional security layers when using Modbus in critical systems, especially in environments where cyber threats are prevalent.
Can Modbus be used for wireless communication?
Yes, Modbus can be used for wireless communication, although it requires some adaptation. While the traditional Modbus protocol operates over wired connections (RS-485, RS-232, Ethernet), wireless communication can be enabled by using Modbus gateways that convert the protocol to run over Wi-Fi, Bluetooth, or other wireless standards.
Wireless Modbus setups are typically used in applications where running physical cables is impractical, such as in remote monitoring systems or mobile industrial equipment. Examples of wireless Modbus solutions include:
- Modbus over Wi-Fi: Useful in factory automation for wirelessly monitoring machines and devices.
- Modbus over Bluetooth: Ideal for short-range communication between devices in a small area. However, wireless communication introduces latency and potential security risks, so it’s important to assess the network’s reliability and implement strong security measures.