Lead vs Lead Free Solder – A Detailed Analysis
Introduction
When it comes to soldering, one of the key decisions you need to make is whether to use leaded or lead-free solder. Both options have their advantages and disadvantages, and it’s important to understand the differences before making a choice. In this article, we will explore the pros and cons of leaded and lead-free solder, and help you determine which one is the right choice for your specific needs.
What is Lead Solder?
Lead solder, also known as tin-lead solder, is a type of solder that contains a mixture of tin and lead. The most common composition of lead solder is 60% tin and 40% lead, although other ratios are also used depending on the specific application. Lead solder has been widely used for decades in various industries, including electronics, plumbing, and automotive.

Lead solder has several properties that make it desirable for soldering. It has a low melting point, which allows it to flow easily and create strong bonds between components. It also has good wetting properties, meaning it spreads evenly across the surface of the materials being soldered. Additionally, lead solder is relatively inexpensive and readily available.
The Environmental and Health Concerns of Lead Solder
While lead solder has been widely used in the past, there are significant environmental and health concerns associated with its use. Lead is a toxic substance that can have serious negative effects on human health, particularly in high concentrations or with prolonged exposure. It can cause neurological damage, developmental issues in children, and various other health problems.
Lead solder also poses environmental risks. When disposed of improperly, lead can leach into soil and water, contaminating ecosystems and posing a threat to wildlife. Furthermore, the production and disposal of lead solder contribute to air pollution and greenhouse gas emissions.
Advantages of leaded solder
There are several advantages to using leaded solder:
- Lower melting point: Leaded solder has a lower melting point compared to lead-free solder, which makes it easier to work with, especially for beginners.
- Better wetting: Leaded solder has better wetting properties, meaning it spreads more easily across the surfaces being soldered, resulting in stronger and more reliable connections.
- Less prone to cold joints: Cold joints, which occur when the solder doesn’t fully bond with the components, are less common with leaded solder.
- Less expensive: Leaded solder is generally less expensive than lead-free solder, making it a cost-effective option for many applications.
Disadvantages of leaded solder
Despite its advantages, leaded solder also has some drawbacks:
- Environmental concerns: The main drawback of leaded solder is its environmental impact. Lead is a toxic substance that can be harmful to both humans and the environment if not handled and disposed of properly.
- Regulatory restrictions: Due to the potential health risks associated with lead, there are strict regulations in place regarding its use in certain industries, such as electronics manufacturing.
- Health risks: When working with leaded solder, it’s important to take proper safety precautions to minimize the risk of lead exposure. This includes wearing appropriate protective gear and ensuring proper ventilation in the workspace.
What is Lead-Free Solder?
Lead-free solder is a type of solder that does not contain any lead. Instead, it is typically made with a combination of tin, silver, and copper, along with other elements depending on the specific formulation. The most common composition of lead-free solder is 96.5% tin, 3% silver, and 0.5% copper.
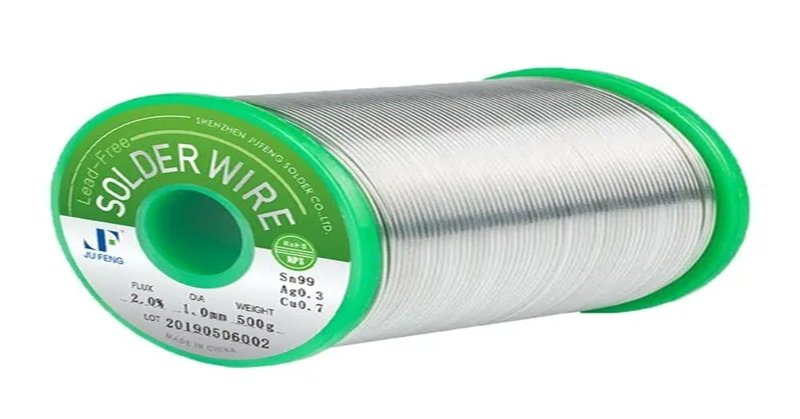
Lead-free solder offers several advantages over lead solder. Firstly, it is safer for both human health and the environment. By eliminating lead from the solder, the risk of lead poisoning and environmental contamination is significantly reduced. Lead-free solder also complies with various regulations and standards, such as the Restriction of Hazardous Substances (RoHS) directive.
Additionally, lead-free solder has comparable or even superior performance to lead solder. It has good thermal and electrical conductivity, ensuring reliable connections. Lead-free solder also has a higher melting point, which can be advantageous in applications where high temperatures are involved.
Why Choose Lead-Free Solder?
There are several reasons why you should consider using lead-free solder for your soldering projects:
- Health and Safety: By using lead-free solder, you are protecting yourself and others from the harmful effects of lead exposure. This is particularly important if you are working in a poorly ventilated area or frequently soldering.
- Environmental Responsibility: Lead-free solder is more environmentally friendly, as it reduces the risk of lead contamination in soil, water, and air. By choosing lead-free solder, you are contributing to a cleaner and healthier planet.
- Regulatory Compliance: Many countries have regulations in place that restrict the use of lead solder in certain applications. By using lead-free solder, you ensure compliance with these regulations and avoid potential legal issues.
- Performance and Reliability: Lead-free solder offers comparable or even better performance than lead solder, making it suitable for a wide range of applications. It provides reliable connections and has good thermal and electrical conductivity.
- Availability: Lead-free solder is readily available and widely used in various industries. You can easily find lead-free solder in different forms, such as wire, paste, or preforms, depending on your specific soldering needs.
Types of Lead Free Solder
Lead-free solder is a type of solder that does not contain lead, which was commonly used in soldering in the past. Due to environmental concerns and health risks associated with lead, lead-free solder has become the preferred choice for many industries. In this article, we will explore the different types of lead-free solder and their applications.
Tin-Silver-Copper (SAC) Solder
One of the most popular types of lead-free solder is Tin-Silver-Copper (SAC) solder. It is composed of tin, silver, and copper, which are mixed in various ratios depending on the specific application. SAC solder offers excellent thermal and mechanical properties, making it suitable for a wide range of electronic applications.
SAC solder is commonly used in the electronics industry for soldering surface mount components, such as printed circuit boards (PCBs), as well as through-hole components. It provides good wetting and flow characteristics, ensuring reliable solder joints. SAC solder also has a lower melting point compared to traditional lead-based solder, making it easier to work with.
Tin-Copper (SnCu) Solder
Another type of lead-free solder is Tin-Copper (SnCu) solder. It is composed of tin and copper, with varying percentages of each metal depending on the desired properties. SnCu solder is often used in plumbing, HVAC, and automotive applications.
SnCu solder offers good thermal conductivity and high tensile strength, making it suitable for joining copper pipes and fittings. It also has a lower melting point compared to SAC solder, which can be advantageous in certain applications where lower temperatures are required.
Tin-Zinc (SnZn) Solder
Tin-Zinc (SnZn) solder is another type of lead-free solder that is commonly used in the electronics industry. It is composed of tin and zinc, with varying percentages of each metal depending on the specific application. SnZn solder is often used for soldering components that are sensitive to high temperatures, such as heat-sensitive electronic components.
SnZn solder has a relatively low melting point, which helps prevent damage to delicate components during the soldering process. It also offers good wetting properties, ensuring reliable solder joints. SnZn solder is commonly used in applications such as mobile phones, laptops, and other electronic devices.
Other Types of Lead-Free Solder
In addition to SAC, SnCu, and SnZn solder, there are several other types of lead-free solder available in the market. These include Tin-Bismuth (SnBi) solder, Tin-Silver (SnAg) solder, and Tin-Silver-Copper-Bismuth (SACB) solder.
Tin-Bismuth (SnBi) solder is commonly used in low-temperature applications, such as soldering heat-sensitive components. It has a low melting point and offers good wetting properties.
Tin-Silver (SnAg) solder is widely used in the electronics industry for applications that require high reliability and thermal stability. It offers excellent wetting properties and is often used for soldering critical electronic components.
Tin-Silver-Copper-Bismuth (SACB) solder is a variant of SAC solder that includes bismuth as an additional alloying element. It offers improved thermal fatigue resistance and reduced void formation, making it suitable for high-reliability applications.
Key Differences Between Lead and Lead-Free Solder
1. Composition: Lead solder contains a significant amount of lead, usually around 60% or more, while lead-free solder is primarily composed of tin, silver, and copper. The absence of lead in lead-free solder makes it a safer alternative.
2. Melting Point: Lead solder has a lower melting point compared to lead-free solder. This lower melting point allows for easier application and rework. Lead-free solder, on the other hand, requires higher temperatures for proper melting and bonding.
3. Environmental Impact: Lead solder poses a significant risk to the environment due to the potential for lead contamination in soil and water. Lead-free solder reduces this risk and helps to minimize the environmental impact of electronic waste.
4. Health Concerns: Lead is a toxic substance that can cause various health issues, especially when inhaled or ingested. Lead-free solder eliminates the risk of lead exposure, making it safer for both workers and end-users.
5. Reliability: While lead solder has been used for many years and has proven to be reliable, lead-free solder has also shown excellent performance in terms of mechanical strength and electrical conductivity. Advances in lead-free solder technology have made it a viable alternative to lead solder.
Advantages of lead-free solder
There are several advantages to using lead-free solder:
- Environmental friendliness: Lead-free solder is considered to be more environmentally friendly compared to leaded solder. It eliminates the risk of lead contamination in the environment.
- Compliance with regulations: Lead-free solder is compliant with various regulations and standards, making it the preferred choice in industries where the use of lead is restricted or banned.
- Health benefits: By eliminating lead from the soldering process, lead-free solder reduces the risk of lead exposure, protecting the health of both workers and end-users.
Disadvantages of lead-free solder
While lead-free solder offers many benefits, it also has some downsides:
- Higher melting point: Lead-free solder generally has a higher melting point compared to leaded solder, which can make it more challenging to work with, especially for beginners.
- Reduced wetting: Lead-free solder may have reduced wetting properties, meaning it doesn’t spread as easily as leaded solder. This can result in weaker solder joints if not properly managed.
- Higher cost: Lead-free solder is typically more expensive than leaded solder due to the higher cost of the materials used in its composition.
Which solder should you use?
The choice between leaded and lead-free solder ultimately depends on your specific needs and circumstances. Here are a few factors to consider:
- Regulations: If you work in an industry that has strict regulations regarding the use of lead, such as electronics manufacturing, lead-free solder is likely the only option for you.
- Environmental impact: If you prioritize environmental friendliness and want to minimize the risk of lead contamination, lead-free solder is the way to go.
- Experience level: If you are a beginner or have limited soldering experience, leaded solder may be easier to work with due to its lower melting point and better wetting properties.
- Cost: If cost is a major consideration for your project, leaded solder may be the more affordable option.
Conclusion
Finally we can say, Leaded and lead-free solder both have their advantages and disadvantages, and the choice between the two depends on various factors. If you prioritize ease of use, lower cost, and are not restricted by regulations, leaded solder may be the right choice for you. On the other hand, if you are concerned about the environment, compliance with regulations, and the health risks associated with lead, lead-free solder is the way to go. Ultimately, it’s important to weigh the pros and cons and make an informed decision based on your specific needs and circumstances.